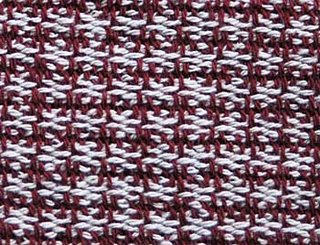
This is another nice one - a six-shaft crepe weave. The interesting thing about crepe weave is that it is threaded as a straight draw: just 1-2-3-4-5-6 repeated. The magic is in the tie-up. This is another structure that lends itself to long warps - imagine all the things you can do with that threading and just by changing the tie-up and treadling, you could weave 25 different towels.
Sharon Alderman, in
Mastering Weave Structures, has a great section on crepe weaves. This is another one that needs more than four shafts to work well. It's fun to design new crepe structures (they're probably not really new but they're fun anyway). There is a technique called "dicing" that is used here. You start with a 3x3 tie-up section and then reflect it as if looking in a mirror but also use the opposite harnesses - tie up those that were not tied up in the original.
It's too hard to explain without pictures but if you look up "dicing" you should find an explanation that would be better than I can give here. In any case, by starting with different 3x3 sections for the lower left corner of the tie-up, you end up with a different 6x6 tie-up which may or may not work as another crepe structure. I hope this isn't more than you wanted to know.
Anyhow, the idea behind crepe is to have small warp and weft floats but also to have a pattern that isn't regular so you get texture without a noticeable pattern. The picture here uses two colors but you can also get nice fabric with just one color and let the texture stand out more. As with many of these towels, this one is 8/2 cotton at 20 epi. To get good crepe, you need a very consistent beat, so you may want to weave one whole towel before taking a break. Also, if you use a yarn that is more tightly spun, the crepe texture will stand out more. It's a little like lace - the threads under the floats collapse to make the texture.
I also should have noted on my last post that the threading for honeycomb is the same as for Monk's Belt.
I got my warp on the Dorothy today and started weaving. I'll post pictures after I've woven a bit more. I'm happy to say that the loom is working well. On the other hand, it's a table loom and I just don't like table looms. It's one of those things, though, I feel that I need one for workshops and weaving demos, but I surely don't plan on doing a lot of weaving on it.